Constantly looking for the best formulation
A look behind the scenes at Selectline, producer of line marking products
At first glance, there may not seem to be much to it: the lines on sports fields. But there is a lot involved in the development of high-quality, wear-resistant sports field lines. Producer Selectline gives a look behind the scenes at the R&D department in Baarle-Nassau, where developments are carried out on a daily basis in order to produce even better products. At first glance, there may not seem to be much to it: the lines on sports fields. But there is a lot involved in the development of high-quality, wear-resistant sports field lines. Producer Selectline gives a look behind the scenes at the R&D department in Baarle-Nassau, where developments are carried out on a daily basis in order to produce even better products. The name Selectline may not ring a bell with Dutch Groundsman, but it is one of the largest producers of line marking paint in Western Europe. Selectline is part of the Smartcoat Group, to which Sudlac and Redusystems also belong. The company has its origins in Horticulture, developing functional coatings to optimise the climate and efficiency in greenhouses. After more than 30 years of experience in the development and production of line marking paint, a dedicated team has been working for the Selectline brand since 2018. Selectline supplies products for sports field lines in approximately 25 countries, mostly for private labels. In the Netherlands, Selectline cooperates with Rofraline, under whose name the products are sold. Because of this, Selectline has got a low brand awareness. But the company wants to change this now. The ambition is to grow. Jeroen Vrieselaar, Commercial Manager at Selectline, explains: Our ambition is to become much bigger in line marking, with a focus on Western Europe. We want to achieve this by continuing to do what we are good at: delivering high quality products, together with good service to our customers. Distributors who only go for the lowest price are not in the right place with us. We prefer to work on long-term relationships. A journey to become a dealer with us can take two or three years. We see our dealers as partners and visit them several times a year. For us, line marking paint does not mean shipping pallets, but working closely with the market. What makes Selectline unique is that it manages the entire process of supplying line marking paints itself. In Baarle-Nassau there is a factory for production and a Lab with a Research & Development team. There is also a factory and research lab in Grenoble, France. This is a major advantage, explains Vrieselaar: Because we have our own factory, we have full control over production and do not need to buy in from outside. With us, customers can always count on receiving exactly the same product with the delivery times they are used to. We can always fulfil our agreements. The R&D department is the basis for the products. Roel Weijers is the R&D Manager at the Smartcoat Group. Under his supervision, a team is working full-time to optimize Selectline's line marking products. Because, contrary to what a Groundsman might suspect, there is a lot more to line marking paint than 'just drawing a white line'. Weijers: 'A line must be as white as possible, but the consumption must also be as low as possible. That is a challenge; during development, you see that all kinds of aspects are important. How the product flows, for example: whether it covers the entire blade of grass and whether you need a lot of it to turn the grass white. These are all aspects that we pay attention to in connection with performance. We are always interested in developments by suppliers that can help us to make our lines as white as possible. At R&D, this translates into testing new formulations, in which the ingredients are different every time. Weijers: 'We always try to find a balance between whiteness and which raw materials are needed for that. We know, for example, that titanium dioxide has a high whitening power, but it is also an expensive raw material, so the costs of the product increase. Another challenge is the ready-to-use products, widely used in the Netherlands, where the product can be used straight from the jerrycan. It must be so thick that the pigment sets very slowly. If only a little pressure is then applied, the coating must lose its viscosity and become easy to spray. You need very specific components to achieve this. Product development is one of the main tasks of the R&D team. Weijers explains how a new product is developed from the beginning to the end: 'First, the formulation is produced on a small scale in the laboratory, half a litre, and tested on the test field next to the factory. Here the product is sprayed and compared to the reference, to check whether it is whiter. Differences in flow, quality and resistance to wear after a shower are also examined. If that looks good, we make a larger quantity of 10 litres and apply that to the grass as well. Next to this it is also important to know: how does the product perform if you don't use it for six months? There are big differences and it takes a lot of time to test this. We also look at the workability: how long do you have to shake before the product can be applied homogeneously? All these factors have to be better than in the reference. Before we take the final step, we make a test production. The product is then presented to the clubs in a controlled way and we do a quality check over a certain period, also taking into account the feedback from the sport clubs. Vrieselaar adds: 'Sometimes it is nice to be the first with something, but we prefer the product to be tested for 200%. That takes time. Our R&D department has high standards. An important question is how you can assess whiteness in an objective way. Weijers: 'In the laboratory we can measure colours very well, but outside, when the product is applied on the grass, it is almost impossible to do that. It can make a difference to your opinion of a product whether you look at a line in the walking direction or in the opposite direction. That does make it challenging. At Selectline, it is therefore customary to perform regular blind tests: lines are assessed without the assessor knowing which product was used to lay them. At the moment, the R&D department is testing new raw materials, among other things, because of the current raw materials crisis. If a certain manufacturer cannot supply an ingredient, it is necessary to have an alternative on hand. On the day of our visit, just such a test is being carried out. Marloes Bijleveld, Product Developer of the R&D department, is outside testing alternative formulations. There are several lines on the Selectline court. 'You can see here that we have lined up with our current product (the reference) alongside products made with alternatives to the raw materials that are used as standard. We are now examining whether these raw materials are suitable to serve as back-up in the event of an emergency', explains Bijleveld. The application involves spraying with different nozzles. The smallest nozzles are the most critical and therefore the starting point. Because customers sometimes use them in practice. So we always start from the most difficult variant. Once on the field, Bijleveld notes whether the products meet the requirements: do the products made with alternative raw materials have the same whiteness and sprayability? After a rain shower, we check whether the lines are still good; then we decide whether a raw material can be a worthy alternative. The R&D department also plays a major role in the final production. Each raw material is checked for quality before it can be used in production. As soon as R&D gives its approval, the factory knows that the raw materials in question may be used for the production of the line marking products. Of every batch of line marking products, R&D carries out another quality check. A sample of each batch produced is checked for a number of specific properties. After approval, the product is released and may be delivered to the customer No batch or raw material is skipped,' says Weijers. We check 100% of all incoming raw materials and outgoing products. In the Laboratory, there are jars with test samples that are kept for one to two years, depending on the product. The advantage of this is that Selectline always has a sample to follow the development in time. Customer questions are therefore easy to answer. Because how well a line marking product is received depends on more than one factor. Vrieselaar: 'It is a combination of the line marking paint, line marking machine, type of pump and nozzle. The whole system contributes to the result'. The Groundsman has also got an important role, because the walking speed can influence the consumption. Anyone who would like to test Selectline's line marking products is invited to contact us," says Vrieselaar. Our distributors and we ourselves are happy to visit you and show you our products. It is important that users can see it with their own eyes.A look behind the scenes at Selectline, producer of line marking products
Everything under one roof
Balance
High standards
A quality check is carried out on al the line marking products manufactured
Daily testing
Quality control
'The whole system contributes to an optimal result'
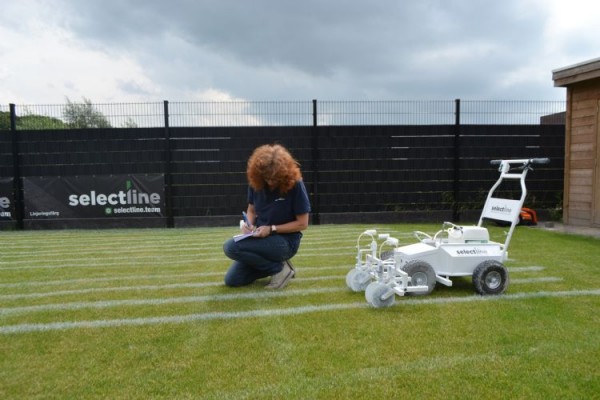